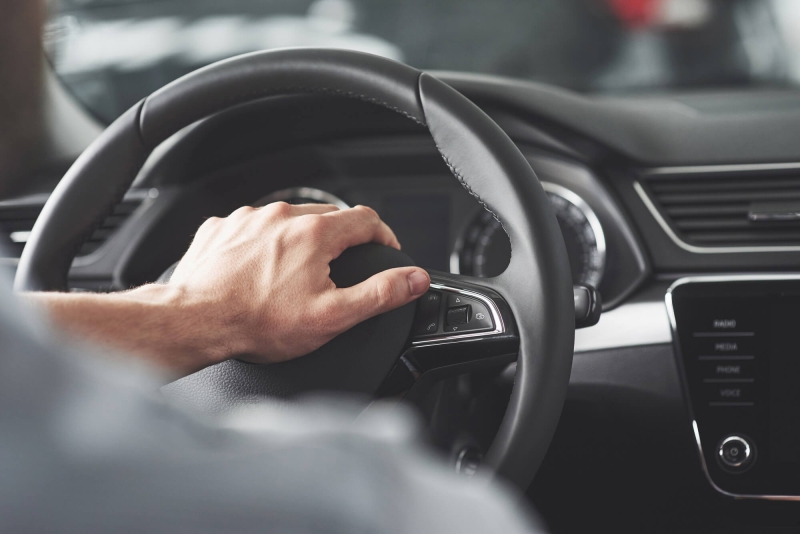
Types of Plastics Used in the Automotive Industry, and their Applications
Today, automotive plastics are making a big difference in the manufacture of automotive parts. Below are the most common ones used in the industry and their applications.
Polypropylene (PP)
Polypropylene is a semi-crystalline, durable, high-performance plastic polymer. It is highly chemical and heat resistant and highly moldable. Consequently, it is suitable for manufacturing products with complex designs. Additionally, PPA chemical and heat tolerance makes it great for automotive parts.
Polypropylene is a widely applicable plastic in automobiles because of its ability to adapt to many plastic manufacturing techniques and its chemical and heat resistance. Therefore, it is critical to manufacture the following automotive parts and components:
- bumper
- gas cans
- engine covers
- cable insulation
- instrument panels
Polyurethanes (PUR)
Polyurethane is another high-performance plastic polymer made from bonded urethane. Its diverse shapes make it a versatile automotive plastic, suitable for both complex and simple automotive components. Consequently, polyurethane is a common plastic polymer subjected to plastic manufacturing processes for automotive parts, such as injection molding and CNC machining.
In addition to its versatility, polyurethane is highly suitable for industry due to its insulating properties, strength, resilience and moldability. Therefore, polyurethane is applicable in the manufacture of parts and components that protect the noise and heat of engines and parts that require resistance in the bodywork. Examples of automotive parts and components made with the polymer include:
- passengers
- headrests
- Soundproofing and air filtration systems
- bumper
- suspension insulators
- tires
Polyvinyl Chloride (PVC or Vinyl)
PVC is a common commercial plastic polymer with wide acceptance in the automotive industrial environment, known for its excellent chemical and water resistance, inexpensive accessibility, impact resistance, durability and brittleness.
PVC has low heat stability, requiring additives to improve its properties. Consequently, there is a reduction in the number of compatible products for which it is suitable. However, it is applicable in manufacturing the following components and parts.
- vehicle airbags
- door panels
- cables
- Panel
- Protection of the underside of the upholstery
Acrylonitrile Butadiene Styrene (ABS)
ABS is a high performance automotive thermoplastic and amorphous polymer composed of three monomers; acrylonitrile, butadiene and styrene and manufactured using ABS injection molding. Its monomer units determine its physical and mechanical properties. However, the polymer is strong, durable and has good electrical insulating properties.
ABS is dyeable, which makes it more aesthetically pleasing. Therefore, it is applicable in the manufacture of components such as:
- Dashboards
- body parts
- wheel covers
Polyethylene terephthalate (PET)
Polyethylene terephthalate is a relatively safe automotive plastic with a glass-like appearance and a high strength-to-weight ratio. In addition, it is flexible, resistant to moisture and does not emit odors or smoke. Therefore, it is applicable in the manufacture of outer body parts and housing, engine covers, connector housing and headlight retainer.
Acrylonitrile Styrene Acrylate (ASA)
ASA is an amorphous thermoplastic similar to ABS but with greater water resistance and greater resistance to heat, chemicals and wear. Furthermore, ASA is insoluble in water with good dimensional stability and weldability. That's why it is applicable in manufacturing parts and components such as instrument panels, interiors and electrical parts.